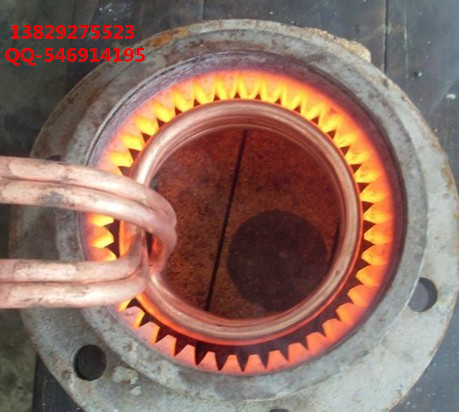
卧式淬火机床在关键零部件热处理中的核心作用与技术解析
在现代制造业中,螺纹轴、钢棒、导轨、齿条等零部件作为机械设备的核心传动与承重部件,其表面硬度、耐磨性及抗疲劳性能直接决定了设备的可靠性与寿命。卧式淬火机床通过精准感应加热、可控冷却及自动化工艺集成,成为提升这些零部件性能的关键装备。以下是其技术优势、应用场景及实际效益的全面分析:
一、卧式淬火机床的技术优势
精准控温与局部硬化
高频/中频感应加热:根据工件尺寸选择频率(1-300kHz),实现表面快速升温(如螺纹轴齿部3秒内达900℃),硬化层深度可控(0.5-5mm)。
闭环温控系统:红外测温仪实时反馈,温度误差≤±5℃,避免过烧或欠热。
均匀性与变形控制
卧式旋转淬火:工件水平旋转(10-60rpm),配合多线圈分段加热,确保周向硬度差<2HRC(如导轨表面硬度HRC58-62)。
仿形冷却系统:针对齿条、螺纹等复杂轮廓,定制喷淋头实现均匀冷却,变形量<0.1mm/m。
高效节能与自动化
连续作业能力:集成上下料机械臂,单件处理时间≤2分钟(传统井式炉需30分钟以上),产能提升15倍。
能耗优化:电能利用率>85%,较盐浴淬火节能50%以上,无废盐污染。
二、典型零部件淬火工艺参数与效果
零部件 | 材料 | 工艺参数 | 性能提升效果 |
螺纹轴 | 40Cr(调质钢) | 频率100kHz,功率50kW,加热8秒,水淬 | 齿面硬度HRC58-60,耐磨性提升3倍 |
导轨 | GCr15(轴承钢) | 频率50kHz,功率80kW,加热15秒,油淬 | 表面硬度HRC60-62,寿命延长至5万小时 |
齿条 | 20CrMnTi(渗碳钢) | 渗碳后高频淬火(频率200kHz,加热5秒) | 芯部韧性HRC30-35,表面硬度HRC58-60 |
钢棒 | 45钢(中碳钢) | 中频淬火(3kHz,功率120kW),层深3mm | 抗弯强度提升40%,疲劳极限达600MPa |
三、与传统工艺的对比优势
指标 | 卧式淬火机床 | 箱式炉整体淬火 | 火焰淬火 |
能耗(单件) | 1-5kWh(按尺寸) | 10-20kWh | 燃气成本等效8-15kWh |
硬度均匀性 | HRC波动≤2 | HRC波动>5 | HRC波动>10 |
变形控制 | 直线度误差<0.1mm/m | 变形量0.5-2mm/m | 局部变形不可控 |
环保性 | 无污染,冷却液循环使用 | 盐浴废气需处理 | CO、NOx排放超标 |
四、经济性与投资回报分析
成本节约
能耗:年处理10万件工件,较箱式炉节省电费超50万元(按0.8元/kWh计)。
材料:氧化损耗从1%降至0.2%(氮气保护),年省钢材成本20-50万元。
效率提升
产能:单台设备日处理量达500-800件,减少设备闲置与库存压力。
人工:自动化产线减少3-5名操作员,年省人力成本30-50万元。
投资回报周期
设备成本:标准机型80-200万元(按功率配置)。
回本周期:1.5-2年(按中型企业年产值5000万元计算)。
五、行业应用案例
案例:数控机床导轨高频淬火升级
背景:某机床厂导轨原采用火焰淬火,表面硬度不均(HRC50-58),磨损导致精度下降。
方案:引入卧式淬火机床(100kW,50kHz),定制仿形感应线圈+聚合物冷却系统。
成果:
导轨硬度HRC60-62,直线度误差<0.05mm/m,装机寿命提升至8年(原3-4年)。
年节省返修成本200万元,客户订单增长30%。
结论
卧式淬火机床通过精准、高效、环保的工艺特性,为螺纹轴、导轨等关键零部件赋予了卓越的表面性能,彻底解决了传统热处理工艺的质量波动与效率瓶颈。其技术优势不仅体现在硬度与寿命的提升上,更通过自动化与节能设计推动了制造业的绿色转型与成本优化。对于追求高可靠性、低维护成本的设备制造商,投资卧式淬火机床是实现竞争力跃升的战略选择。