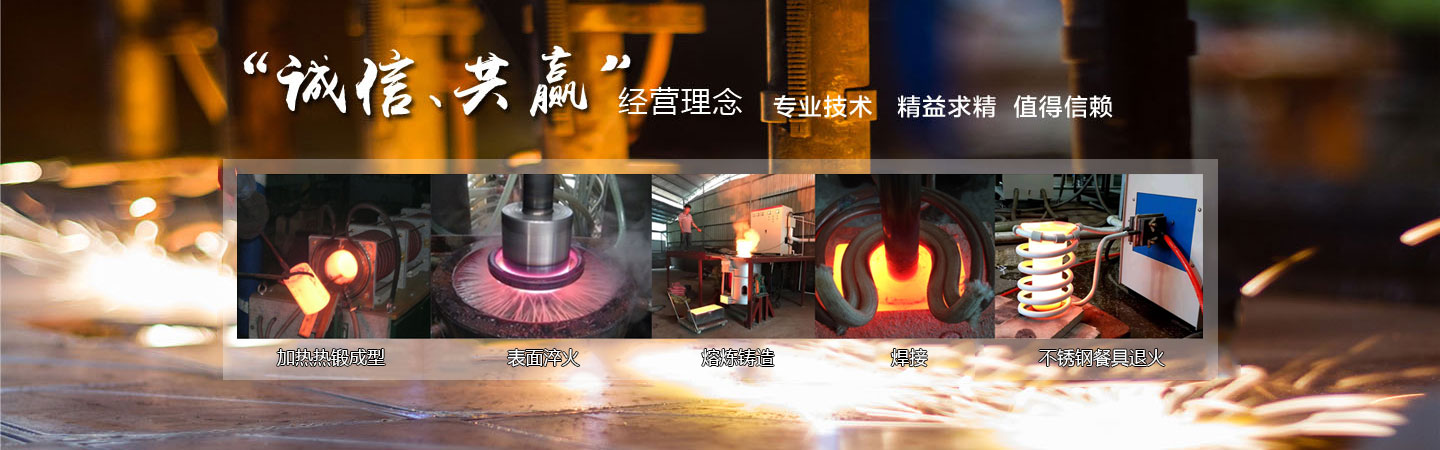
在现代金属加工领域,淬火工艺作为提升金属工件性能的关键环节,其重要性不言而喻。而自动化淬火设备的出现,更是为这一传统工艺注入了新的活力,凭借其集成的高频感应加热技术、自动化控制技术以及先进的淬火工艺,成为了众多金属加工企业的得力助手,在实现对金属工件快速、精确淬火处理方面展现出了卓越的优势。
一、高频感应加热技术 —— 快速加热的核心原理
自动化淬火设备之所以能够实现快速淬火,关键在于其所集成的高频感应加热技术。这一技术基于电磁感应原理运作,当设备启动后,高频电流通过特制的感应线圈,瞬间会在其周围产生高频交变磁场。将金属工件放置在这个磁场中时,工件内部会因电磁感应而迅速产生强大的涡流,由于金属自身具有电阻,涡流在流动过程中便快速将电能转化为热能,使得工件能够在极短时间内升温至淬火所需的温度范围。
例如,对于一些小型的金属零部件,传统的加热方式可能需要较长时间才能达到淬火温度,而借助自动化淬火设备的高频感应加热技术,仅需短短几十秒甚至几秒的时间,就能完成加热过程。这种快速加热的特性,不仅极大地缩短了单个工件的淬火周期,而且在批量生产时,能够显著提高整体的生产效率,满足现代制造业对于高效生产的迫切需求。
二、自动化控制技术 —— 精确淬火的保障
自动化控制技术是自动化淬火设备的又一重要支撑,它为精确淬火处理提供了坚实的保障。通过先进的控制系统,操作人员可以在设备操作界面上轻松设定各种淬火参数,如加热功率、加热时间、淬火冷却介质的流量与温度、工件的移动速度与旋转角度等,这些参数都能够根据不同金属工件的材质、尺寸以及具体的淬火工艺要求进行精准调整。
在淬火过程中,自动化控制系统会实时监测和调控设备的运行状态,确保各个环节严格按照预设的参数执行。比如,当工件加热到预定温度时,系统会精确控制冷却环节的启动时间和冷却速度,保证淬火冷却过程的及时性和稳定性,使工件能够形成理想的淬火组织,获得预期的硬度、韧性等性能指标。而且,由于整个淬火过程是由自动化系统精确把控的,避免了人为操作可能带来的误差和不确定性,无论是对同一批次还是不同批次的金属工件,都能确保淬火质量的稳定性和一致性,这对于生产高质量的金属产品至关重要。
三、先进的淬火工艺 —— 提升淬火效果的关键
自动化淬火设备还融合了各类先进的淬火工艺,进一步提升了淬火处理的效果。它能够根据不同工件的形状、结构以及使用要求,灵活选择合适的淬火方式,如整体淬火、局部淬火、表面淬火、穿透淬火等。
以汽车发动机中的曲轴为例,其结构复杂,不同部位对于硬度和韧性的要求各不相同。自动化淬火设备可以针对曲轴的轴颈、曲柄等关键部位,采用局部淬火工艺,通过调整感应线圈的形状和位置以及相应的参数设置,精确地对这些部位进行加热淬火,在提高轴颈表面硬度以增强耐磨性的同时,保证曲柄部位具备足够的韧性来承受复杂的交变载荷,从而优化曲轴的整体性能,延长其使用寿命。
又如,对于一些对表面硬度要求较高的精密机械零件,设备可以实施表面淬火工艺,使工件表面形成一层硬度高、耐磨性好的淬火层,而内部依然保持良好的韧性,这样既能满足零件在工作过程中对表面耐磨的需求,又能防止因整体过硬而出现脆断的情况,实现了性能的完美平衡。
四、自动化淬火设备在生产中的综合优势
提高生产效率
自动化淬火设备的快速加热能力和自动化操作流程,使其在单位时间内能够处理更多的金属工件。在批量生产场景下,无需人工频繁地干预每一个工件的淬火过程,设备可以连续稳定地运行,大大缩短了生产周期。与传统的手动或半自动化淬火设备相比,生产效率能够提升数倍甚至更高,这对于满足大规模订单需求以及提高企业的市场竞争力有着积极的影响。
确保产品质量稳定一致
如前文所述,自动化控制技术和先进淬火工艺的结合,确保了每一个经过淬火处理的金属工件都能达到相同的质量标准。无论是硬度、耐磨性、韧性等性能指标,还是工件的尺寸精度、外观质量等方面,都能保持高度的稳定性和一致性。这不仅减少了因质量问题导致的产品返工和报废情况,降低了生产成本,还提升了企业产品的品牌形象,增强了客户对产品的信赖度。
适应多样化生产需求
在实际的金属加工生产中,工件的种类繁多,材质、形状、尺寸以及淬火要求各不相同。自动化淬火设备凭借其高度的灵活性和可调节性,能够轻松应对这种多样化的生产需求。只需简单地调整参数、更换感应线圈或者选择不同的淬火工艺,就可以对各种金属工件进行淬火处理,无需购置多台不同类型的淬火设备,提高了设备的利用率,也为企业节省了设备投资成本。
总之,自动化淬火设备以其集成的高频感应加热技术、自动化控制技术以及先进的淬火工艺,在金属工件淬火处理方面展现出了强大的优势,实现了快速、精确淬火,提高了生产效率,确保了产品质量的稳定性和一致性,适应了多样化的生产需求。随着制造业不断朝着智能化、高效化的方向发展,自动化淬火设备必将在金属加工领域发挥越来越重要的作用,为行业的发展提供有力的技术支撑。